The availability of continuous-duty air-cooled compressors (particularly in large sizes) offers a great deal of flexibility for installing them. Such compressors can be mounted on any surface that will support their static weight. In many facilities, great savings also are available in piping cost, compared to other types of systems. These compressors lend themselves to either the central- or departmental-compressor system concept. Units are available with electric motor and engine drives - on bases, on skids, on wheels, etc.
Compared to other types of continuous-duty air compressors, oil-cooled rotary-screw compressors offer a number of advantages:
- Oil cooling holds internal temperatures to an optimum level. As a result, discharge air is relatively cool -no more than about 180° F higher than ambient.
- Discharge air is clean - free from burned oil or carbon.
- The rotary design lends itself to higher speeds, particularly in the larger sizes. Consequently, larger flow capacity is available from compressors with physically smaller envelopes - providing significant savings on floor space and foundation requirements.
- Because of their compact size and inherent quiet-running characteristics, it is relatively easy to suppress noise. Electric-motor-driven models are commercially available rated from 75 to 85 dB at one meter per the CAGI Pneurop Test Code.
- Most models have fewer moving parts, and those parts run under more ideal conditions - resulting in lower temperatures and less vibration.
- Fewer parts make it easier to stock them for the rotary designs, and the machines are easier to work on.
In summary, oil-cooled rotary-screw compressors offer users a continuous-duty source of compressed air in a neat, compact package that has low initial cost, maximum flexibility of installation, and easy maintenance.
Non-lubricated rotary screw and lobe:
In addition to the non-lubricated reciprocating compressors that have become so common over the years, there are several versions of non-lubricated positive-displacement lobe or screw rotary compressors. These units are referred to as clearance-type compressors because the internal parts do not contact each other, so they require no lubrication in the compression chamber. Cooling is accomplished through the cylinder walls via water jackets.
The lobes or screws do not drive one another either; they are driven by some type of gear arrangement instead. This drive system also acts as a timing gear to maintain the rotor or lobe profile relationship accurately. Lubricant for the drive train must be confined to the bearing and gear area - and not allowed to get into the compression chamber.
In this basic design, there is a constant leakage rate for any fixed set of conditions. The critical internal clearances are between end covers and the rotor, between the rotor lobes, and between the rotor OD and the cylinder ID. These gaps, combined with no injected oil to help with sealing, are the main reasons why two stages are required for these units to produce acceptable efficiencies in 100-psi class applications.
Because these are rotary units, they enjoy all the advantages of rotaries over similar-sized non-lubricated reciprocating units:
- compact size,
- smooth delivery of cool air,
- ease of installation, and
- simple (but critical) maintenance
They also have some disadvantages, depending on the specific type of compressor and its duty cycle:
- more sensitive to dirty inlet air,
- lower efficiency - resulting in higher power cost, and
- any repair work is more sophisticated and requires specialized training, which the user may not have nor want to have. This means repair work will probably have to be performed by the distributor or the manufacturer.
Sliding-vane rotary compressors:
Oil-cooled sliding-vane compressors, Figure 2, operate as other positive-displacement compressors do by trapping a charge of intake air - in this case, between the vanes. As the eccentric rotor turns, the vanes are forced into the rotor slots, shrinking the size of the cell holding the trapped air. The air is compressed to full discharge pressure when it reaches the outlet port. The heat of compression is removed by cooling oil sprayed right into the air while it is being compressed. The same oil helps with sealing the vane tips.
For decades, oil-cooled, sliding-vane rotary compressors have been popular for continuous-duty applications. Their design has a number of unique characteristics:
- light weight - yet continuous rating,
- integrated and compact configuration,
- efficient production of compressed air at relatively low rotary speeds,
- smooth operation with little vibration,
- extremely quiet operation,
- coolest possible discharge air, and
- few wearing parts, making the machine easy and economical to repair.
However, the oil-cooled rotary-vane design in its single-stage configuration is limited in capacity. Bending stress applied to the vanes is the problem. The speed, size, and weight of the vanes must be limited for the machine to be durable. Because of this, oil-cooled rotary-vane compressors generally are applied only in a size range between 2 and 100 hp.
Lubricated or lube-free?
Two fundamental groups of compressor types are lubricated and lube-free. Lubricated compressors use oil to reduce friction between moving parts. As a result, some oil is entrained in the air being compressed. The entrained oil must be removed from or tolerated by the downstream system.
Lube-free compressors use no oil in the airend, and thus add no oil to the compressed air they produce.
Power and efficiency:
Brake horsepower is the input power required at the compressor input shaft for a specific speed, capacity, and pressure condition.
Motor or engine horsepower is the nominal rating of the prime mover.
The service factor is the additional power built into an electric motor above its nominal rating - expressed as percent. Within the service factor, the brake horsepower driving an air compressor can be higher than the motor's nominal horsepower.
The power efficiency of a compressor is the ratio of the air delivered by the compressor and its input electrical requirements. Efficiency usually is expressed as brake horsepower per 100 cfm of delivered air.
Water-cooled rotary screws:
Another version of oil-free rotary-screw compressors is a single-stage design that uses water injection to cool and seal the rotors during compression. The bearings and drive gears are lubricated with oil and sealed from the compression chamber. These units serve a selected market and are a special design. In some applications, care must be taken to avoid the build-up of bacteria in the water.
Dynamic air compressors:
Dynamic, or centrifugal compressors, Figure 3, are dissimilar to the positive-displacement machines already discussed because they raise the pressure of air by converting the energy of its velocity into pressure. First, rapidly rotating impellers (similar to fans) accelerate the air. Then, the fast flowing air passes through a diffuser section that converts its velocity head into pressure by directing it into a volute.
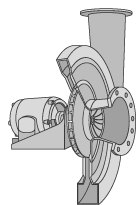
Because the centrifugal is a mass flow compressor, it has a limited stable operating range. This has a large effect on economic operation or bhp/100 cfm delivered at part load. Minimum turn-down capacities for centrifugals may vary from 20% to 30% of full load, depending on impeller design, number of stages, etc.
There are limits to the pressure rise that can be achieved in a single stage by a centrifugal compressor - due to both physical and economical restraints - so two- to four-stage units are built that incorporate one to three water-cooled intercoolers. Cooling the air between stages reduces the power required to compress the air further, resulting in more efficient operation. Intercooling actually may permit the desired compression to be accomplished in fewer stages.
The centrifugal compressor is definitely a continuous-duty unit because its service life is unaffected by full-load operation. However, it is also a relatively sensitive machine because it operates at high speeds - often as high as 50,000 rpm. Ambient factors which affect flow are altitude, inlet air temperature, and the relative humidity of inlet air. The operating life of this type of unit is primarily determined by the amount of entrained liquids and solids carried into the unit at the inlet - and the quality of the cooling water. As in all machinery, correct installation and maintenance is critical to the efficient production of compressed air and reaching a satisfactory operating life.
When a facility requires a continuous-duty, high-volume (2,000 to 25,000 cfm) supply of non-lubricated air, the centrifugal compressor is one of the best choices. In fact, it is the only choice in sizes above 1,000 hp. Whether or not it fits the installation best is another question to be answered after analyzing the job conditions. In any event, when correctly applied, installed, and maintained, a centrifugal compressor offers a reliable, continuous source of compressed air.
Advantages and disadvantages:
After reviewing the comments on air compressors in this article, one conclusion is fairly obvious: each design has advantages and disadvantages which must be matched to a specific application. The table on this page summarizes a number of selection factors for the most common basic designs. Other factors, such as air quality and installation requirements, are difficult to quantify. The unavoidable cost factor - initial, operating, and maintenance - is noted with them in the following text.
Double-acting reciprocating - Advantages: highest efficiency, longest service life, field serviceability. Disadvantages: highest initial cost, high installation cost, high maintenance cost.
Oil-flooded, single-stage rotary screw - Advantages: low initial cost, low maintenance cost, packaged design. Disadvantage: low efficiency.
Oil-flooded, two-stage rotary screw - Advantages: higher efficiency, simple packaged design, same low maintenance cost. Disadvantage: higher initial cost.
Oil-free rotary screw - Advantages: high-quality air, moderate efficiency, simple packaged design. Disadvantage: higher initial cost.
Centrifugal - Advantages: the only type available above 600 hp, high-quality air, moderate efficiency, longer service life than other rotaries. Disadvantages: higher initial cost, must be water cooled, air flow is sensitive to changes in ambient conditions.
Importance of capacity controls:
Many compressed-air conservation program on the demand side target such issues as:
- identifying and repairing air leaks,
- eliminating open blowing,
- fixing malfunctioning condensate drains, and
- managing all potential inappropriate uses.
When these programs are completed successfully, often it is found that the facility consumes less compressed air for production, but electrical energy consumption does not go down proportionally. The reason: without appropriate capacity controls operating correctly on compressors, it is impossible to effectively translate lower air use into lower electrical energy input.
When working effectively, compressor-unloading controls should:
- match air supply to demand when needed,
- eliminate or minimize system overpressure,
- maintain the necessary minimum acceptable operating system pressure,
- reduce the input power cost to the optimum point proportional to the air flow demand, and
- turn off unneeded air compressors and bring them back on when required.
Regardless of the type of air compressor, the operating principles of capacity controls can be grouped into several basic categories. (Note that some will only perform on certain types of compressors.) Here are descriptions of these categories with some of the pros and cons of each.
Automatic start-stop control - This control simply starts and stops the electric motor or driver automatically. It can operate any type of compressor. A pressure switch usually accomplishes this function, shutting off the motor at the upper pressure limit, restarting it at the minimum system pressure.
Pro: the air compressor runs at its two most efficient modes, fully loaded and off.
Con: most AC electric motors can survive only a finite number of starts over a given time frame, primarily due to heat build up. This limits the application of automatic start-stop controls - particularly for motors larger than 10 to 25 hp.
Con: the compressor must run above minimum system pressure to hold that pressure.
Con: the system must have adequate air-storage capacity to perform satisfactorily.
Continuous-run controls (step type) - With these controls, the driver or electric motor runs continuously while the air compressor is unloaded in some manner to match supply to demand. System pressure usually commands the unloading arrangement. Continuous-run controls can be categorized as step or modulating type.
The most common is the two-step control which holds the compressor inlet either fully open or fully shut. Over the complete operational band, the compressor runs fully loaded (or at full flow) from the preset minimum pressure (or load point) to the preset maximum pressure (or no-load point). At the latter, the control shuts off air flow completely. The unit then runs at no flow and full idle until system pressure falls back to the load point. The control then goes immediately to full-flow capacity. A pressure switch typically actuates the two-step control, which can be either the primary control or part of a dual-control system on virtually every type of air compressor. (Some reciprocating compressors can be fitted with 3- and 5-step controls.)
Pro: the compressor runs at its two most efficient modes - full load and full idle - which results in the lowest possible input power cost. Full idle at lowest input power is accomplished almost immediately, except in the case of lubricated or lubricant-cooled rotary-screw compressors.
Con: both correct piping and adequate air storage are necessary to allow enough idle time over the operational pressure band to generate any significant energy savings.
Con: when two-step controls are misapplied, not only is there little or no power cost savings, but short cycling (i.e.: 20 sec. on/ 20 sec. off) can damage the equipment and shorten the life of normal wearing parts.
Con: too much backpressure in the interconnecting system can cause short cycling or ineffective unloading.
Con: at 85% to 95% loads, step controls consume some extra power because they have to compress at full capacity to a higher pressure just to hold a lower design system pressures.
Continuous-run controls (modulating) - These controls match supply to demand very accurately all along the operating band pressure range. Most incorporate some type of regulator, which in effect converts the operating pressure control band into a proportional band. If system pressure fluctuates as little as 1 psi, the modulating control immediately decreases or increases flow proportionally, depending on the signal. (This control generally is installed only on lubricant-cooled rotary-screw and centrifugal compressors.)
Pro: the minimum set system pressure draws the most power. As system demand falls, pressure rises, flow cuts back, and power usage also falls. This results in a savings at higher demand (and is the opposite of 2-step unloading where the power draw actually increases as system demand falls).
Pro: more efficient at high loads.
Pro: holds a relatively steady pressure when demand is stable, and responds responds quickly to any change.
Pro: does not depend on storage capacity to operate effectively.
Con: is generally more inefficient at lower loads.
Con: too much backpressure in the interconnecting piping can force multiple units into running on part load, when one or more could be shut off.
Controls for rotary screws:
Industry's most commonly used air compressor in sizes above 30 hp today is the lubricant-cooled rotary-screw compressor. A significant number (80% to 85%) of these compressors use some form of modulating control as the primary unloading control or as the upper-range portion of a dual control. Two types of these controls for oil-injected rotary-screw compressors are throttled inlet and variable displacement.
In a throttled inlet control, the compressor's inlet valve is opened or closed to match supply to demand as sensed by a pressure regulator. The inlet valve modulates continuously and responds immediately in to any change in the sensed system pressure. In effect, flow capacity is controlled by restricting air intake. The control holds a constant system pressure with minimal valve movement at any given steady system demand.
Pro: smooth, non-cycling control of system pressure is easier on the power train and most other components.
Pro: is relatively efficient at loads from 60% to 100%.
Pro: will not short cycle, regardless of storage capacity and or piping.
Pro: simple to operate and maintain.
Pro: usually results in lower lubricant carryover in lubricated units.
Con: relatively inefficient at loads below 60%.
Con: backpressure must be overcome in order to reach full capacity.
Con: instant response may make the machine back down and unload, even when flow is needed for the base load.
Con: sensitivity and rapid reaction make correct piping and backpressure control necessary for optimum operation. (Note: this is true for all types of unloading controls).
Variable-displacement controls:
These controls for rotary-screw compressors all match output to demand by modifying or controlling the effective length of the rotor compression volume. The inlet pressure remains the same throughout the turn down, and the compression ratio stays relatively stable. This method of reducing flow without increasing compression ratios has a power advantage over modulating and/or 2-step controls in the operating range from 50% to full load.
The two most common of these unloading controls are the spiral-cut high lead valve and the poppet valve. Both methods open or close selected ports in the compressor cylinder, thus changing the seal-off points. These ports are located at the start of the compression cycle where pressure is very low. Opening them even a small amount prevents compression from occurring until the rotor tip passes the cylinder bore casing that separates the ports. This effectively reduces the trapped volume of air to be compressed and consequently the horsepower needed to compress it.
Pro: very efficient part-load performance from 50% to 100%.
Pro: maintains set pressure at minimum system pressure. Pro: very responsive.
Con: at higher loads, some units lose efficiency due to increased leakage.
Con: the mechanism is complex.
Con: still must run 2-step or modulation in lower operating range.
Variable-speed drives:
Variable-speed drives (VSDs) control the speed of the prime mover. In theory, the performance unloading curve for compressors powered by VSDs is very attractive. Depending on the type of compressor, model, conditions, etc., unloading can be almost optimal in the range from 50% or 60% to 90% of load - i.e.: 75% power could produce close to 75% flow. Variable-speed turbines and engines have proved effective for years on all types of compressors. These drives maintain system pressure at the minimum set point and will modulate back as soon as the sensed system pressure raises.
In the world of electric motors, the most commonly applied VSD has been the variable-frequency driver (VFD) - usually as a retrofit or part of a special package. VFDs convert 60-Hz alternating current to direct current, and then reconvert it to AC at the frequency required to turn the motor at the desired speed. This conversion usually consumes about 2% to 4% more energy, and therefore VFDs are less efficient at full load than other types of controls.
Many VFDs have been installed successfully on lubricant-cooled rotary-screw compressor packages over the years, but there are some areas of concern that have limited their economies relative to cost and overall performance - particularly in retrofits. First, the design of some rotary-screw compressors causes efficiency to drop at less than full-load speed. Second, changing speeds can produce harmonic amplification problems that were not considered at the original design speed. Third, the motor itself may have efficiency problems at the low end of the speed range, possibly because of inadequate heat rejection and cooling capacity. Compressors with air ends designed specifically for VFDs will eliminate or minimize many of these potential problems.
Switched-reluctance VSDs:
Another type of VSD being offered is the switched-reluctance system. This electrical control converts standard 3-phase AC power into 2-phase DC. The rectified AC voltage is passed to a bank of capacitors where it is increased to 600-V DC and stored. The bank then supplies the power required by each phase of a brushless motor, eliminating surge currents in the main power supply. The brushless motor has the inherent ability to survive an unlimited number of starts and stops per hour because the absence of inrush current surges keeps its operating temperature low.
The true application for any compressor with a VSD should be as a trim machine, not as the plant air system's base-load unit.
Where to put it:
Industrial air compressors are rugged machines that will perform under adverse conditions, but it always is advisable to provide proper operating conditions to maximize reliability at minimum operating cost. Traditionally, compressors have been located in separate rooms to isolate their noise. Such locations are almost mandatory today to meet OSHA requirements. However, it still is important that the compressor room have an adequate foundation (particularly for reciprocating machines) as well as ample space so that the machine is easily accessible for inspection and maintenance. Stairways and catwalks can assist these procedures on larger compressors.
The compressor room ideally should be clean and dry. Auxiliary equipment, piping, and wiring should be arranged so that it does not interfere with routine inspections. Instruments should be located within easy view of operators.
Partial summary of air compressor selection factors - 100 psig service |
Type | Capacity in scfm | Horsepower | Cooling medium | Lubrication |
Reciprocating | <1 to 3,018 | <1 to 600 | <100 hp - Air >75 hp - Water | For some models |
Single-stage, lubricated rotary | 14 to 3,000 | 5 to 700 | Air or water | Yes |
Two-stage, lubricated rotary | 560 to 3,100 | 100 to 600 | Air or water | Yes |
Dry rotary | 75 to 4,200 | 40 to 900 | Air or water | No |
Centrifugal | 400 to 25,000 | 125 to 6,000 | Water only | No |
Applicability of air compressor unloading controls |
Type of control | Lubricant-cooled rotary screw | Oil-free rotary screw | Reciprocating (single-acting) | Reciprocating (double-acting) | Centrifugal |
Automatic start-stop | Yes | Yes | Yes | Yes | Yes |
Two step Three and five step | Yes No | Yes No | Yes No | Yes Yes | Yes (dual) No |
Throttled inlet Variable displacement | Yes Yes | No No | No No | No No | Yes N/A |
Variable speed | Yes | No | No | No | No |
!!!THANK YOU FOR READING THIS POST!!!